Request a free evaluation of your file to receive a tailored strategy for reducing your occupational health and safety costs.
Prevention is the key to reducing the number of accidents, their severity and the associated costs (lost time, equipment breakdowns, etc.). DR Conseils provides expert guidance through a program designed to reduce both direct and indirect costs by promoting prevention in the workplace.
DR Conseils offers a wide range of prevention services
Outsourcing
DR Conseils offers comprehensive occupational health and safety outsourcing services tailored to the needs of each organization. From supporting OHS committees and developing emergency action plans to training employees and representing companies before the authorities, our team delivers personalized assistance at every step. By integrating expertise in prevention, compensation, and legal compliance, we offer proactive, tailored solutions to ensure your compliance with the latest regulations.
DR Conseils can meet all your OHS needs, including:
- OHS committee support
- Training for employees and managers on various OHS topics
- Emergency response plan implementation
- Risk analysis
- Policy and procedure drafting
- Coaching for managers
- Accident investigations
- WHMIS implementation
- Industrial hygiene
- Statistical analysis of workplace accidents
- Representation with CNESST inspectors and CLSCs
- Safety inspection and audit implementation
- Recommendations on various prevention topics
Our health and safety team consists of some twenty people, including specialized prevention consultants, compensation advisors, and litigators. This team works closely with legal specialists, ensuring we remain at the forefront of regulatory interpretation and new health and safety provisions.
As part of our commitment to quality, DR Conseils consistently assigns the same team members to each project, ensuring clients receive consistent follow-up and high-quality interventions. We believe that strong interpersonal relationships are key to project success, which is why we prioritize continuity by maintaining a stable team throughout the process.
Production of lockout sheets
To ensure worker safety during maintenance operations, lockout sheets must be created. These sheets clearly identify the type of operation to be performed, the energy sources present, and the associated risks. In compliance with safety standards*, they provide detailed, step-by-step instructions and include explanatory images to minimize the risk of accidents related to hazardous energies. This course will guide you through the process of creating lockout sheets to ensure they meet all regulatory and safety requirements.
Contents :
- Equipment identification
- Identification of energy sources (electrical, mechanical, hydraulic, etc.)
- Identification of isolation devices
- Equipment labeling
- Steps to follow to deactivate equipment
- Photos of the equipment
* Sections 188.1 to 188.13 of the Regulation respecting occupational health and safety
Adjustment of computer workstations
Office work is part of almost every industry and carries a significant risk: static posture*. Remaining in the same position for extended periods can lead to musculoskeletal disorders. To mitigate these risks, proper workstation adjustments are crucial. That is why we adjust and design your employees’ workspaces to encourage neutral, comfortable and natural posture.
Here are the items and factors to consider when planning adjustments:
- Armchairs
- Work surfaces
- Input devices
- Personal habits
- Monitors
- Accessories
*Static posture involves maintaining the entire body or parts of it in a fixed position for a given period of time. Static effort, even if sometimes unconscious, is essential to maintaining posture.
Fall protection equipment certification
When fall protection is required, a comprehensive program is essential. In this course, we cover all the key components required to develop such a program, from worker awareness and training to equipment selection and adjustment according to the task and user profile. We also explain the importance of regular inspections and certification by a qualified professional and show you how to certify* each piece of equipment, label it correctly, and maintain an up-to-date inspection log.
Here is the list of equipment to be certified:
- Safety harnesses
- Safety lanyards
- Self-retracting lifelines
- Straps
- Winches
- Tripods
*All equipment must be certified to CSA Z259.17.
Respiratory protection program - Administrative measures
The Respiratory Protection Program – Administrative Measures course describes the specific procedures to follow to safeguard worker health and safety when they are exposed to respiratory hazards. In compliance with CSA Standard Z94.4, the program defines key elements such as roles and responsibilities, as well as how to select and maintain respiratory protective equipment (RPE).
The program includes:
- Roles and responsibilities
- Respiratory protection equipment selection
- Identification of appropriate RPE for each hazardous situation
- Maintenance
- Fitting methods
- Program evaluation system
- Training
Respiratory protection program - Identification of respirators
This program is a management tool designed to ensure that respiratory protective equipment (RPE) used in the workplace is correctly matched to the requirements of each situation and provides optimal protection for workers. The program ensures that RPE is properly fitted, worn, maintained and stored. To achieve this, a thorough analysis of each contaminant or hazardous product is essential.
Here is what the analysis should include:
- Identification of contaminants
- Physical state of contaminants
- Exposure threshold for airborne contaminants
- Determination of the concentration of contaminants present
- Oxygen levels in the air
- Presence of an IDLH (immediately dangerous to life or health) atmospheric concentration
- Characteristics of skin or eye absorption
- Other exposure conditions
Respiratory protection fit testing
Respiratory protection equipment fit training is designed to protect workers against airborne contaminants such as gases, fumes, vapours, dust and mists. Substances such as asbestos, crystalline silica, and various chemicals can pose serious health risks. When these contaminants exceed safe levels, it is essential to implement preventive measures, including the use of respiratory protective equipment (RPE). In this course, we will conduct a qualitative fit test (taste test) for each worker who is required to use a respirator to ensure effective protection against exposure risks.
Company emergency measures and evacuation procedures
The company’s emergency preparedness and evacuation course is designed to equip your organization to handle emergency situations effectively, safeguarding the lives of your employees, protecting your assets, and securing your future. To achieve this, developing a comprehensive emergency response plan is crucial for ensuring the success of your prevention program.
This plan should include:
- Roles and responsibilities
- Building description
- Fire detection, protection and alarm systems
- Working hours
- Assembly point
- Evacuation procedures (if applicable):
- Fire
- Managing aggressive people
- Bomb alert
- Active shooter
Occupational health and safety training at the forefront
Workplace accident prevention training has become a key strategy for reducing occupational accidents. Furthermore, to comply with the new health and safety provisions in the Criminal Code, companies must ensure that managers and employees are aware of their respective roles and responsibilities, as well as the prevention measures to be implemented.
An effective health and safety training program is a valuable asset for reducing occupational accidents and illnesses. DR Conseils is a training organization accredited by the Commission des partenaires du marché du travail for the purposes of compliance with the Quebec Act to Promote Workforce Skills Development and Recognition, and training provided by DR Conseils is eligible under the Act, which requires a minimum training investment of 1% of payroll.
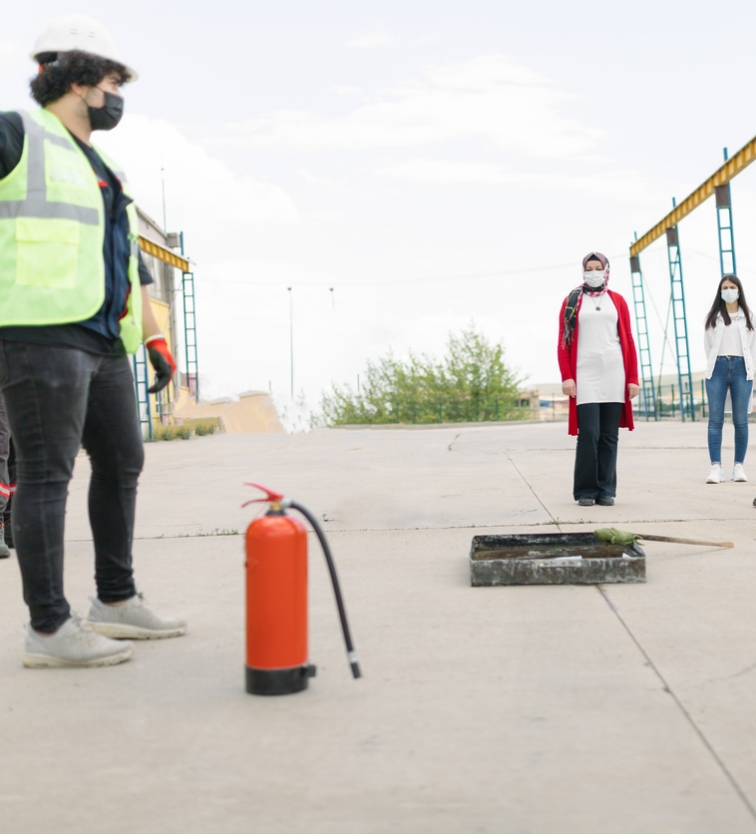
Training tailored to your needs and corporate values
In today’s highly competitive environment, DR Conseils offers training tailored to your needs and corporate values, delivered directly at your employees’ workplaces. We also offer courses to the general public, in which you can enrol your employees.
DR Conseils is a training organization accredited by the Commission des partenaires du marché du travail for the purposes of compliance with the Act to promote workforce skills development and recognition.
DR Conseils offers the following training courses:
Effective health and safety committees (provincial and federal)
This course is aimed at members of occupational health and safety committees who wish to learn more about effective committee management, their responsibilities and best practices in workplace safety.
Content:
- Act respecting occupational health and safety
- OHS committee functions
- OHS communications
- OHS meeting quality
- Planning and running meetings
- Problems and solutions in committee functioning
- Member skills and attitudes
- Success factors
Number of participants: 15
Target audience: Occupational health and safety committee members
OHS awareness and oversight for managers
Content:
- Act respecting occupational health and safety
- Criminal Code
- Stakeholder roles
- Prevention tools
- Prevention program
- Training
- Right of refusal
- Accident investigations
- Complaint follow-up
- Workplace inspection
- Corrective and preventive measures
- OHS disciplinary measures
Number of participants: 15
Target audience: Managers responsible for work teams
Introduction to prevention for new employees
Occupational health and safety is everyone’s concern, whether you are new to your job or not, and whether you are a manager or not.
That is why we offer introductory prevention training for new employees, covering essential topics such as OHS regulations, the use of protective equipment, emergency measures, and much more.
Content:
- Regulations
- Safety risks (depending on the company, choose from the following modules) :
- Personal protective equipment (PPE)
- Handling work
- Adjusting a workstation
- Pedestrian traffic
- Cleanliness and tidiness
- Use of tools and equipment
- Storage/warehousing
- Safe padlocking of equipment
- Use of ladders and stepladders
- Working at heights
- Forklifts
- Confined spaces
- Noise hazards
- Use of hazardous products (WHMIS)
- Emergency measures
- Respiratory protection, respiratory protection selection
*Content may be modified based on risks to contractors inherent to the industry.
Number of participants: 15
Target audience: Any industry employee or manager concerned with health and safety
Introduction to workplace safety inspections
Content:
- What to inspect
- Review of checklists
- Overview of applicable standards
- OHS regulations
- CSA
- National Building Code of Canada
- Rounds of inspection
*Inspection pursuant to the Act respecting occupational health and safety
Number of participants: 15
Target audience: Supervisors, health and safety committee members and employees responsible for inspection
OHS disciplinary measures
Content:
- Act respecting occupational health and safety
- Criminal Code
- Stakeholder roles
- Prevention tools
- Prevention program
- Training
- Right of refusal
- Accident investigations
- Complaint follow-up
- Workplace inspection
- Corrective and preventive measures
- OHS disciplinary measures
Number of participants: 15
Target audience: Managers responsible for work teams
Accident investigation and analysis
Content:
- Objectives
- Definition of a workplace accident
- Who should investigate and when
- Fact-finding during an investigation
- Interviews during an investigation
- Cause analysis and investigation
- Corrective measures and follow-up
- Sample forms and procedures
Number of participants: 15
Target audience: Managers and health and safety committee members.
Psychological risk management
Did you know that psychological health issues are the number one cause of disability claims in the workplace? That is why it is so important to understand psychological risks, know everyone’s rights and responsibilities, and implement preventive measures. By addressing these factors, it is possible to create a healthier and safer working environment where well-being is a priority. This course will focus on strategies to help manage psychological risks in the workplace.
Content:
- Definitions
- Act respecting occupational health and safety
- Employer rights, obligations and responsibilities
- Employee rights, obligations and responsibilities
- Psychosocial risks in the workplace
- Different types of psychosocial risks
- Impact of psychosocial risks
- Identifying risks and solutions
- How to identify a psychological risk
- Applicable preventive measures
- Implementation and evaluation
- Planning implementation
- Assessing the impact of preventive measures
Number of participants: 15
Target audience: Facility managers and prevention officers
Psychological and sexual harassment
Psychological and sexual harassment in the workplace is a serious issue that can have significant consequences for employee health and the work environment. To prevent this type of violence in the workplace, this course will equip you with the necessary tools to recognize, prevent, and effectively manage these situations.
Content:
- Definitions
- Act respecting occupational health and safety
- Employer rights, obligations and responsibilities
- Employee rights, obligations and responsibilities
- Identifying psychological and sexual harassment
- What constitutes harassment
- What does not constitute harassment
- Prevention and intervention
- Raising awareness
- The individual, the manager, and the organization
- Organizational policy
- Steps to take
- Handling complaints
Number of participants: 15
Target audience: Managers and employees
Difficult and aggressive customers
If you or your employees have to deal with difficult or aggressive customers in the course of your work, this course is for you. You will learn how to identify different types of aggression and violence and how to defuse potentially conflictual situations.
Content:
- Recognizing types of aggression and violence
- Legal aspects related to aggression risks
- Steps to take
- Addressing a worker who has been the victim of an act of violence
Number of participants: 15
Target audience: Any employee or manager exposed to difficult and aggressive customers
WHMIS
Do you work with chemical or hazardous products? This WHMIS course will teach you to understand labels, hazard symbols, and safety data sheets. You will also learn how to handle and store these products safely to ensure a safe working environment.
Content:
- Definition of WHMIS
- Purpose of WHMIS
- Laws and regulations
- Obligations of the various stakeholders
- Hazard symbols
- Labels
- Safety data sheets and their categories
- Safe handling and storage
Number of participants: 15
Target audience: Employees who handle hazardous products
WHMIS workplace Instructors
If you are responsible for WHMIS training in your workplace, it is essential to master not only the basics, but also the nuances of this system. This course will help you understand the laws and regulations governing WHMIS, the specific obligations of the various parties involved, and other key elements related to symbol recognition and the handling and storage of hazardous products.
Content:
- Definition of WHMIS
- Purpose of WHMIS
- Laws and regulations
- Obligations of the various stakeholders
- Hazard symbols
- Labels
- Safety data sheets and their categories
- Safe handling and storage
Number of participants: 5
Target audience: Anyone required to provide WHMIS training in the workplace
Respiratory protection (fitting follow-up)
Respiratory protection plays a crucial role in preventing the risks associated with the inhalation of hazardous substances, but such equipment is only effective if it is used correctly. In this course, you will learn how to select the right type of respiratory protection for your working environment, how to adjust it for optimum protection, and how to inspect and maintain it to ensure long-term effectiveness.
Content:
- Choosing respiratory protection
- Protection device parts and inspection
- Cleaning and maintenance
- Donning and fitting
Number of participants: 15
Target audience: Employees required to use respiratory protection in the course of their duties
Instructor - Respiratory protection and fit testing
Becoming a respiratory protection instructor goes beyond understanding the equipment—it is about teaching essential skills to ensure the safety of every employee. This course provides a comprehensive understanding of respirator types, selection criteria for various situations, and fitting and inspection techniques, enabling you to ensure that every team member receives optimal protection.
Content:
- Choosing respiratory protection
- Protection device parts and inspection
- Cleaning and maintenance
- Donning and fitting
Number of participants: 15
Target audience: Anyone responsible for training employees in the use of respiratory protective equipment and for performing fit tests
Safe entry into confined spaces
Working in confined spaces is a high-risk situation that demands constant vigilance, a thorough understanding of hazards, and meticulous preparation. This course will teach you how to plan each entry carefully, considering specific conditions, use protective equipment effectively, and master emergency rescue procedures. Through practical exercises and role-playing, you will gain the skills needed to navigate and manage these hazardous environments.
Content:
- Risks and hazardous environments
- Safe entry procedure
- Confined space entry registers and permits
- Preparing for entry and protective equipment
- Respiratory protection and air quality measurements
- Measuring instruments, their operation and limitations
- Ventilation
- Supervisor’s role and rescue
- Practical exercise and simulation
Number of participants: 15
Target audience: Employees required to work in confined spaces
Safe lockout procedures
For employees involved in maintenance, repair, unlocking, or inspection tasks, it is essential to know how to control hazardous energy sources. This course will teach you when and why to use lockout procedures, how to identify hazardous energy sources, and how to implement safety procedures. Through case studies and equipment demonstrations, you will learn how to prevent accidents and create a safer working environment.
Content:
- Reasons for lockout
- Risks related to energy sources
- Energization: primary and secondary energy sources, types of energy involved
- When to lock out
- Lockout regulations
- Description of the procedure before and after work, single lockout, multiple lockouts, forgotten locks
- Equipment presentation
- Case studies
Number of participants: 15
Target audience: Employees involved in maintenance, repair, unlocking, or inspection work involving energy sources that activate processes, equipment or machines
Prevention when working a height
Working at height presents significant risks. How can you make sure you are fully prepared to face these challenges? Our working at height course covers all the critical safety aspects, from understanding regulations and identifying risks to mastering the use of protective equipment such as harnesses and anchor points. Through hands-on exercises, you will also learn how to assess fall distances, inspect your equipment before each use, and much more.
Content:
- Regulations
- Risks
- Protective devices
- Anchor points
- Connections
- Safety harnesses
- Effectiveness of protection devices (video demonstration)
- Free falls
- Calculating total fall distance
- Equipment inspection
- How to put on a harness
- Practical exercise
Number of participants: 15
Target audience: Employees who may be required to work more than three meters above the ground
Safe load handling
Lifting, moving and handling loads are common tasks, but if not done correctly, they can lead to serious injuries. Our safe load handling course offers a practical approach to minimizing these risks. Learn how to adjust your workstation, adopt proper lifting techniques, use ergonomic equipment, and more to ensure safe and efficient handling practices.
Content:
- Regulations
- Understanding anatomy and physiology
- Environmental risks
- Ergonomic intervention approach
- Equipment to facilitate handling
- Basic handling principles (grip, posture, movement)
- Workstation adjustment and practical exercises
*Content may be modified to take industry-specific risks to contractors into account.
Number of participants: 15
Target group: All employees required to handle loads
Forklifts
Do you use a forklift? This course will guide you through key elements such as checking equipment, understanding stability and driving principles, and much more.
Content:
- Regulations, driving issues and internal policies for forklift drivers
- Statistics
- Truck classifications
- Equipment nameplates
- Forklift checklist
- Principles of forklift stability
- Principles of driving and operating equipment
- Centre pivot and restricted space
- Stacking/unstacking (pile) and storage (pallet rack)
- Handling
- Truck loading and unloading
- Propane tank replacement and/or battery charging and replacement on equipment
Number of participants: 6
Target Audience: Forklift operators, forklift mechanics, managers
Safe excavation work
Excavation work involves specific risks, such as the potential for wall collapse and hazards related to underground utilities. To minimize these risks, it is important to follow strict safety protocols and understand legal requirements. This course will teach you how to assess hazards, correctly operate earthmoving equipment, and apply shoring techniques to ensure safe and compliant excavation practices.
Content:
- Risk of wall collapse
- Legal obligations
- Safety procedures
- Excavation, digging and trenching
- Earthmoving equipment used for digging
- Safe excavation near underground pipes
- Shoring rules
Number of participants: 15
Target audience: Any employee required to perform excavation or trenching work
Asbestos risk awareness
Asbestos, still found in many buildings, poses serious health risks. This course will teach you how to identify asbestos-containing materials, assess the level of risk on worksites, and correctly use protective equipment to ensure safety.
Content:
- Origin and properties of asbestos
- History of asbestos use in buildings
- Materials likely to contain asbestos
- Health effects and toxicity of different types of asbestos
- Asbestos regulations
- Risky working conditions according to the Safety Code for the construction industry (low, moderate and high)
- Personal and respiratory protective equipment
- Presentation of the glove bag
- Importance of an asbestos management program
Number of participants: 15
Target audience: Employees handling asbestos-containing materials
Working in a hot environment
Did you know that working in a hot environment presents hazards such as toxic fumes, burns and electric shock? This course covers key regulations, essential safety practices, and the proper use of WHMIS. It also prepares you to handle emergency situations, ensuring a safer working environment.
Content
- Objectives
- Definitions
- Standards and regulations
- Statistics
- Risks
- Fumes and gases
- Electricity
- Burns
- Radiation
- Noise
- Ergonomics
- WHMIS
- Emergency situations
Number of participants: 15
Target audience: Any employee required to work in a hot environment